Electro-galvanizing and hot-dip galvanizing
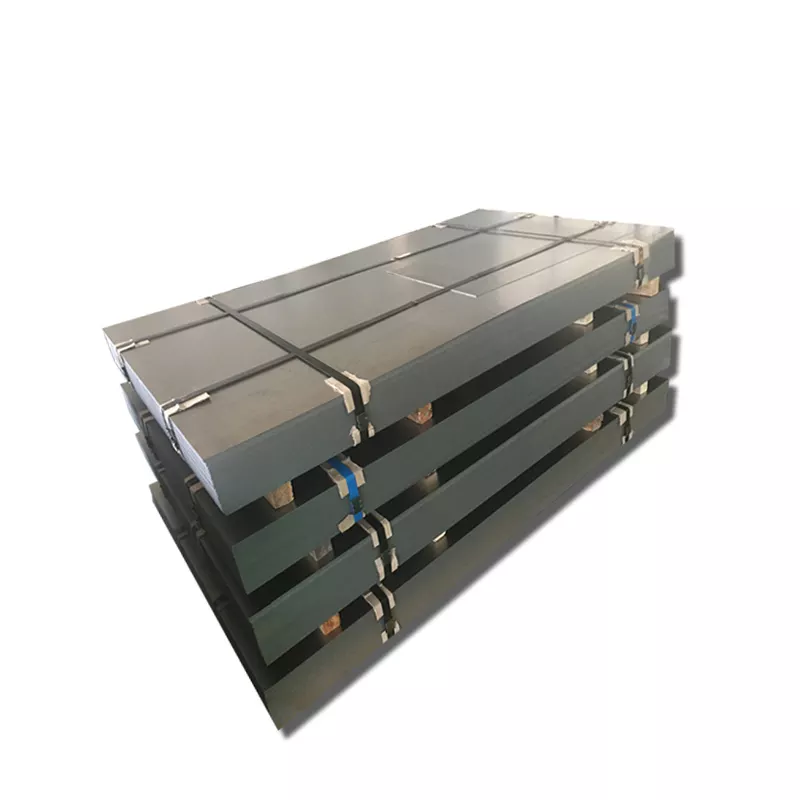
There are obvious differences between electro-galvanizing and hot-dip galvanizing in terms of process principles, appearance quality, corrosion resistance and service life.
Process principle: Electrolytic zinc plating uses electrolytic deposition method for galvanizing. It needs to be surface treated first, and then immersed in the electrolyte for electroplating. Hot-dip galvanizing is to immerse metal steel in molten zinc for galvanizing. The process is relatively simple, has a wider application range, and the coating is uniform and the thickness can reach 50~100 microns.
Appearance quality: The thickness of electro-galvanized coating is thinner, the appearance is smoother, and it has better appearance quality and is suitable for manufacturing fine small parts. The coating of hot-dip galvanizing is thicker and rougher in appearance, but it is thick, strong and wear-resistant. The surface can be uneven, making the galvanized steel more textured.
Corrosion resistance: Hot-dip galvanizing has better corrosion resistance because its thick coating can form a protective film to effectively protect the substrate. The corrosion performance of electroplated zinc is relatively poor, and surface treatment is generally required to enhance its anti-corrosion ability.
Service life: Since hot-dip galvanizing has better corrosion resistance, it also has greater advantages in service life. In some harsh environments, hot-dip galvanized steel can be used for a long time without corrosion. The service life of electro-galvanized steel is relatively short. If it is used in humid, corrosive and other environments, it is prone to surface rust and delamination.
In general, electro-galvanizing and hot-dip galvanizing each have their own characteristics, and they can be selected according to specific needs and conditions when choosing to use them.
Process principle: Electrolytic zinc plating uses electrolytic deposition method for galvanizing. It needs to be surface treated first, and then immersed in the electrolyte for electroplating. Hot-dip galvanizing is to immerse metal steel in molten zinc for galvanizing. The process is relatively simple, has a wider application range, and the coating is uniform and the thickness can reach 50~100 microns.
Appearance quality: The thickness of electro-galvanized coating is thinner, the appearance is smoother, and it has better appearance quality and is suitable for manufacturing fine small parts. The coating of hot-dip galvanizing is thicker and rougher in appearance, but it is thick, strong and wear-resistant. The surface can be uneven, making the galvanized steel more textured.
Corrosion resistance: Hot-dip galvanizing has better corrosion resistance because its thick coating can form a protective film to effectively protect the substrate. The corrosion performance of electroplated zinc is relatively poor, and surface treatment is generally required to enhance its anti-corrosion ability.
Service life: Since hot-dip galvanizing has better corrosion resistance, it also has greater advantages in service life. In some harsh environments, hot-dip galvanized steel can be used for a long time without corrosion. The service life of electro-galvanized steel is relatively short. If it is used in humid, corrosive and other environments, it is prone to surface rust and delamination.
In general, electro-galvanizing and hot-dip galvanizing each have their own characteristics, and they can be selected according to specific needs and conditions when choosing to use them.
Related Products
Factory Introduction
316N Stainless Steel Product Introduction
High temperature resistance of 304 and 316 stainless steel
Contact Us