316 stainless steel mirror coil with top quality
Simple speaking,stainless steel mirror polishing refers to stainless steel workpiece polished into a mirror.
Mirror polishing process of stainless steel is loose abrasive in the workpiece to be machined surface and basal disc the relative movement of freedom, the surface becomes very high flatness and smoothness, the workpiece does not need strong fixed clamp, vacuum, magnet, is naturally placed on the disc, the base can be suitable for the machining of any metal and non metal materials, not mandatory clamping and rigid grinding grinding machine, reduce the impact and heat generated by the secondary deformation, more conducive to the processing of high precision and finish. Even if an inexperienced operator can easily obtain the ideal polishing effect parallelism roughness can reach up to 0.2um, Ra0.02um. Schematic as follows:
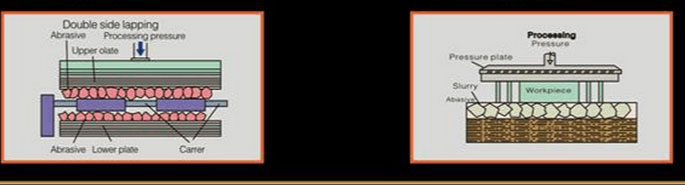
Method of 316 stainless steel mirror coil
Common mirror stainless steel is divided into 6K, 8K, 10K three. General polishing, ordinary 6K, fine grinding 8K, super fine grinding 10K effect. The same thickness of the general is not much difference, 10K mirror brighter; the thicker the thickness, the worse the effect, the higher the cost of processing.
The process of stainless steel mirror polishing is usually divided into three steps: coarse grinding, rough polishing and fine polishing
1)Coarse grinding:aim to lower the size and reach a certain geometric accuracy. The first method is to design according to the stainless steel workpiece fixture is designed to play a fixed role; then installed. And then into the plane grinding machine grinding, due to a variety of stainless steel, according to the specific material to select the grinding disk, grinding fluid.
2)Rough polishing:This procedure is mainly through the bark rough throwing and guide angle 316 stainless steel mirror coil.
3)Fine polishing:The process is easy to product small scratch, so polishing the skin, and the quality of the polishing fluid must be guaranteed, second is the health conditions, to avoid contamination of the grinding fluid, etc., so that employees must pay attention to the details of the operation.
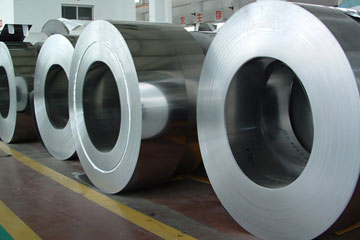
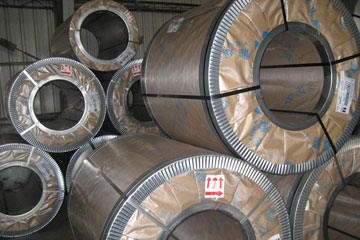
Related Products